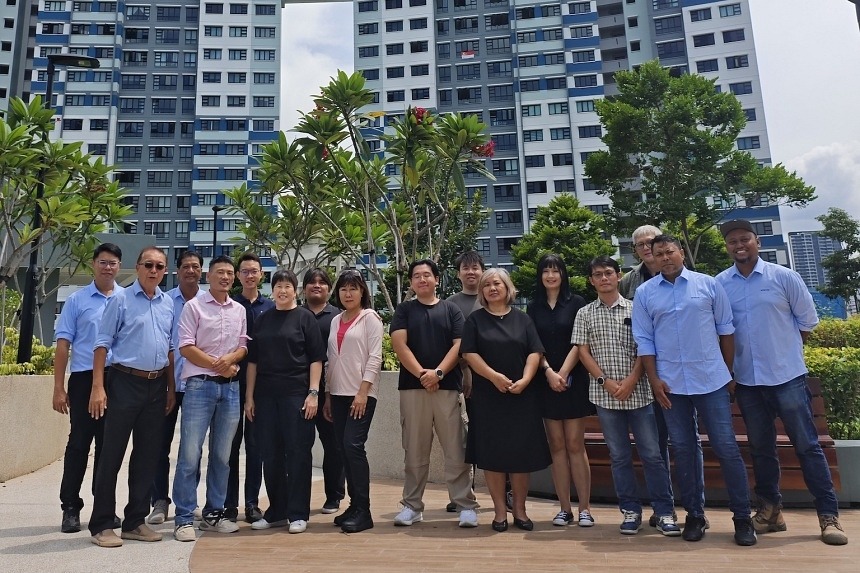
When home owners at West Coast ParkView collected the keys to their flats last year, many breathed a sigh of relief.
The Housing Board (HDB) Build-To-Order (BTO) project, which spans three residential blocks, a multi-storey carpark, link bridges and other amenities, was already delayed by the Covid-19 pandemic when its original contractor became mired in financial difficulties and went bust in 2021 after completing only about 20 per cent of the works.
Although HDB quickly appointed home-grown construction firm Newcon Builders to continue the job, the company faced a daunting task. West Coast ParkView’s project manager He Shuangbiao explains: “To meet HDB’s deadline to hand over the units, we had to bring in experienced sub-contractors and finish the project in two years when what we needed to do would normally take two-and-a-half to three-and-a-half years.”
Other complications arose. There was a construction site for a nursing home nearby, forcing Newcon to share a single access road with the other contractor. “To address this issue, we reached out to the other company and kept in close contact to sequence our works to minimise disruptions,” Mr He shares.
With an eye on the clock, the firm, which was awarded the Construction Resilience Recognition at the HDB Awards 2024, acknowledging the effort of project teams for overcoming pandemic-related challenges, also took other steps big and small to make up ground.
Executing smart moves to save time
As soon as Newcon, which is the main contractor behind Nanyang Technological University’s The Hive building and the Customs Operations Command Complex in Jalan Bahar, came on board, it expedited the hiring of sub-contractors, set up security at the site and sped through other tasks to restart the construction.
With its intense mobilisation of manpower and resources, it resumed the construction works just weeks after taking over the site.
After scrutinising the previous contractor’s plans, it also made changes to save time, without compromising safety. These included switching the typical open-cut method used to excavate ground for the construction of a detention tank, to a faster sheet pile approach, shaving a month off the works.
Instead of building formworks and pouring concrete on site to create the buildings’ lift walls, Newcon adopted a precast method to fabricate these off site and then installed them, reducing the time needed by a third.
To further pick up the pace, the firm dedicated more resources to the project. It engaged two additional pre-casters, for a total of three, to accelerate production of the precast components. It also stockpiled adequate amount of precast components at any given time to ensure uninterrupted progress on the construction.

At the project’s peak, it deployed about 20 per cent more workers on site, to expedite the finishing works to meet HDB’s project handover deadline.
With these and other strategies, Newcon managed to deliver the three residential blocks between two and six weeks ahead of schedule respectively.
Putting residents’ interests first
Newcon also won the Construction Award for its work on Kim Keat Beacon, an HDB BTO project in Toa Payoh that boasts three residential blocks with interconnecting walkways, a landscaped multi-storey carpark and other facilities. The award honours contractors who are outstanding in project management, construction quality, public relations and innovation when undertaking HDB building and upgrading projects.
To deliver Kim Keat Beacon, Newcon overcame numerous challenges, harnessed technologies to help workers and introduced more efficient workflows, says the development’s project manager Mohammed Lukman Omar.
The problems started even before Newcon broke ground. Mr Lukman elaborates: “We were supposed to access the site via a golf course next to it. The course was meant to have been closed by the time we took over the site, but it was still in use, so we had to look for another access point.”
With support from the neighbourhood’s grassroots advisor, the firm developed an alternative plan to use a public road to transport its workers, equipment and materials. Mindful that the road is near a school, it scheduled the trips during class time and had traffic controllers oversee them for safety.
“Since the site is very close to existing HDB blocks, we built noise barriers and went from door to door to give residents notice of the works, assured them that they could contact us if they had any issues, and put feedback forms and our contact number on our hoardings,” the development’s project engineer Johnathon Chng explains.
“When some residents who were working from home for part of the week told us that the construction noise was too loud, we shifted the noisier works to the days when they were in the office.”
Adopting construction and engineering innovations for productivity
Newcon also implemented more efficient ways of working on site. For example, erecting buildings’ lift shafts is usually a lengthy process. Conventionally, a contractor constructs the building up to the roof level before the lift sub-contractor comes in to mark where the lift doors will be in the shaft.
Workers then put up walls to enclose the shaft, leaving space for the doors, and the sub-contractor returns to install the lifts.
“To shorten this process, we worked closely with our lift sub-contractor to give us a clear guideline of where the lift doors will go, while we were still extending the buildings upwards. Our workers then constructed about 80 per cent of the lift walls along with the rest of each floor, so there is less to do at the end,” Mr Chng explains.

The company also equipped workers with electric trolleys to transport more materials more easily and telescopic electric sanders to sand the flats’ surfaces to smooth them in preparation for painting.
With the sander, each worker can sand four units per day, compared to using sandpaper manually which would have taken one day for each unit and is much more laborious.
Looking back, Mr Lim Keh Soon, the project director of West Coast Parkview, highlights the hard work of all involved in the two BTO projects.
He says: “Throughout the challenging pandemic period, our project teams and stakeholders collaborated closely with HDB project teams to ensure the seamless completion of the projects while maintaining stringent standards in project stages, tasks, quality and safety.”